ABB RLM01 PROFIBUS DP/FMS Redundancy Link Module
RLM 01 converts one simple, non-redundant Profibus line into two reciprocallyredundant lines A/B. The module works bidirectionally, which means that all three
interfaces can receive and transmit data.
You can position the module directly after a master, before a bus segment with
several slaves or before an individual slave. PROFIBUS stations with redundant
couplers [K] can be directly connected to the PROFIBUS set redundant by RLM 01.
Stations with only one interface can be optionally assigned to the A or B line. Each
RLM 01 PROFIBUS interface can serve up to 31 PROFIBUS stations. Using
repeaters [R] and media converters [O/E] makes it possible to increase the length of
the PROFIBUS lines and the number of stations.
• Conversion: Line M <=> Lines A/B
• Use on PROFIBUS DP/FMS lines
• Automatic line selection
• Transmission rate 9.6 kBit/s .... 12 MBit/s
• Monitoring of communication
• Repeater functionality
• Redundant power supply
• Status and error display
• Monitoring of the power supply
• Potential-free alarm contact
• Simple assembly on DIN mounting rail
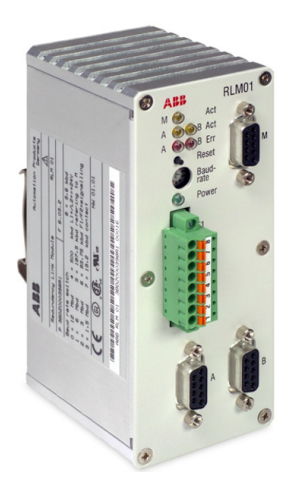
RLM01 does not support master redundancy where one master only runs line A
and the other one only line B. The bus communication is asynchronous, even if
both masters balance their program modules against each other on the
applicational level. A Melody central unitCMC 60/70 offers clock synchronous
communication because of redundant PROFIBUS terminals (A & B).
Network devices like repeater, FOC coupler, DP/PA converter as well as RLM01
cause a N x bit time delay of data telegrams. The delay time (see technical data) is
device specific and depends upon the selected baud rate. It must be taken into
consideration for the master bus configuration.
Section 2 Description of functions
The three RS 485 interfaces of the module support all transmission rates specified in
DIN 19245 for the PROFIBUS from 9.6 kBit/s to 12 MBit/s. The module has
repeater functionality, i.e., it regenerates the signal shape and the amplitude of
received data. RLM 01 monitors all three lines A, B and M for activity and error
states. Detected errors are signalled by lit diodes on the front panel. The potential free alarm contact activated in parallel to this can be polled for diagnostic purposes
by the process control system PCS or by a programmable logic control PLC. The
three serial RS 485 interfaces are potential-free relative to each other and to the
power supply. This is a functional electrical isolation.
The first data coming in over line A or line B with a correct telegram start are routed
to terminal M. With simultaneity, either line A or line B is selected at random.
Testing and selection is always based on the first character. In the case of a telegram
start with error on A, the control logic switches to the redundant line B. The same
procedure applies vice-versa for line B.
Data coming in over line M with a correct telegram start are routed in parallel to the
two terminals A and B. The test for data is always based on the first character. In the
case of a telegram start with error, the control logic does not output any data to A and B.
Either a single or a redundant power supply with 24 VDC is possible. The
distribution of load across L1+ and L2+ is based on the level of the voltages applied.
If a voltage source fails, the switch to the redundant supply source is made without
interruption. A monitoring logic circuit tests whether both voltages are present.
Safety information
To supply RLM 01, use only a safety-low voltage. This requirement also applies to
the alarm contact supply.
In accordance with the UL/CSA requirements an external protection (e.g. fuse) is
prescribed. The fuse rating can amounted to 1.6A to 10A (characteristic: medium
slow-acting or slow-acting). Protection of groups of several devices with a common
fuse is admissible (several RLM 01 or RLM 01 together with other devices).
When selecting a mounting location, make certain that the limit values for ambient
conditions specified in the technical data are observed and the module can discharge
heat without any obstruction.
Do not connect any bus lines that are laid partially or entirely outside buildings.
Voltage overload, for example resulting from lightning strikes, may destroy the
module. For protection against cases such as these, use optical fibre cable and
appropriate medium converters (electrical <==> optical) as high-quality electrical
isolation.
In accordance with the PROFIBUS installation guideline the shielding of the bus
cables are preferably connected at the start and at the end with earth potential. Place
the module on a low-resistance and low-inductance earthed DIN mounting rail.
Grounding measures by way of the E terminal (1) on the terminal strip are then not
required.
Front panel elements
Three Sub-D connectors A, B and M are located on the front panel of the RLM 01
for connection of the PROFIBUS cable. The 8-pin male multi-pin connector with
the associated terminal strip is used to connect the alarm and power supply wires.
There are also LEDs for activity/error display, a rotary switch for setting the
transmission rate and a reset button (activate transmission rate).