GE ZA81L-0001-0083#3C Servo Amplifiers
Servo Amplifiers Motion Control SystemsHigh-Performance Serial Encoders
Standard serial encoders built into the
motors provide exceptional feedback
resolution of 64K or 128K counts per
revolution. Serial encoders support higher
resolutions at high motor velocities than
standard quadrature encoders and
are more immune to noise. An optional
battery connection provides absolute
position feedback, eliminating the need to
home the system after a power shutdown.
Reduced Tuning and Setup
There is no need for potentiometer tuning
or personality modules; little tuning is
required for properly sized drives. All drive
parameters are stored in the controller in
a standard motor database. Configuration
settings are not stored in the drive, making
it possible to replace drives with little
set-up time. Stored drive and machine
parameters are quickly transferred to
repeat production machines.
All-Digital System
All control loops—current, velocity, and
position—are closed in the GE motion
controller. High-speed microprocessors
and/or digital signal processors (DSPs)
in the controller provide loop update
times of 250 µs. The high response servo
system can compensate for machine
design limitations, yielding faster accel eration/deceleration rates and better
responses to load changes.
All-Digital Servo Command Signals
The PACMotion PMM335 motion control lers use a high speed fiber optic command
interface to the αi and βi Series amplifiers.
With its superior noise immunity, both
of these GE digital command interfaces
allows for an increased signal to noise ratio
for improved accuracy and performance.Info
For application, installation, and tuning
information, consult the Services website
at www.ge-ip.com.
Agency Approvals
UL, IEC rating and CE mark compliant
αi and βi Series Servo Amplifiers
All Digital Servo Systems Offer High Performance and Reliability.
GE αi and βi Series Servo Drives, based on over five million axes installed worldwide,
offer superior reliability and performance for unprecedented mean time between
failure. The αi and βi Series Servos are available in a wide range of ratings for use
with GE PACMotion PMM335 Series motion controller.
Series Motor Series Controller Command Continuous Power Supply
Interface Torque RangeIn-lb Nm
αHVi αHVi, αHVis PMM335 Fiber Optic 17.7-1150 2-130 Separate PSM
βi βis PMM335 Fiber Optic 3.5-177 0.4-20 Built-in
βHVi βHVis PMM335 Fiber Optic 17.7-177 2-20 Built-in
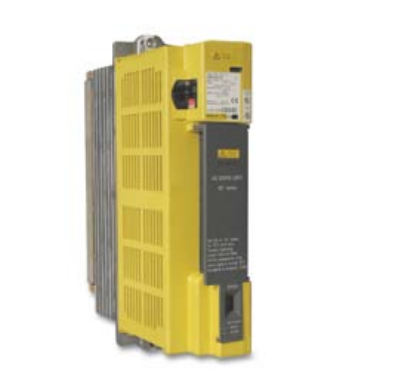
Motion Control Systems
Part Number Description Amplifier Series
ZA81L-0001-0083#3C 5.4 kW, 3-phase AC line filter βi
ZA81L-0001-0101#C 10.5 kW, 3-phase AC line filter βi
ZA81L-0001-0168 5.4 kW, 3-phase AC line filter βHVi
ZA81L-0001-0169 10.5 kW, 3-phase AC line filter βHVi
ZA81L-0001-0163 18kW, 3-phase AC line filter PSM-11HVi, PSM-18HVi
ZA81L-0001-0164 45kW, 3-phase AC line filter PSM-30HVi, PSM-45HVi
The 4A and 20A βi Series Servo ampli fiers can be run on single phase power;
however, the lifetime of the amplifier is
reduced because of higher input and
ripple current. An AC line filter is strongly
recommended to suppress the influences
of high-frequency input line noise on the
drive power supply. If a power source
within the specified voltage range is not
available, a transformer is required. The
kVA rating of the transformer should be
equal to or greater than the sum of all
motor kW ratings. If an isolation-type
power transformer is used, an AC line
filter is not required.
GE offers the following line filters; transformers must be supplied by the user as required.
αi and βi Series Servo Amplifiers
System Power Requirements
Amplifier Specification βi Series αHVi*/βHVi Series
Voltage (-15%, +10%):
3-phase 200-240VAC 400-480VAC
1-phase (see below) 220-240VAC n/a
Frequency 50/60Hz 50/60 Hz
Allowable frequency fluctuation ±2 Hz ±2 Hz
Voltage fluctuation during 7% or less 7% or less
acceleration/deceleration
Ambient Temperature Range 0-55°C 0-55°C
Humidity (non-condensing) 90% 90%
Vibration Less than 0.5G Less than 0.5G Motor Model Max. kW Rating
β0.4/5000 is 0.13
β0.5/6000 is 0.35
β1/6000 is 0.5
β2/4000 is 0.5
β4/4000 is 0.75
β8/3000 is 1.2
β12/3000 is 1.8
β22/2000 is 2.5
β2/4000 HVis 0.5
β4/4000 HVis 0.75
β8/3000 HVis 1.2
β12/3000 HVis 1.8
β22/2000 HVis 2.5
α2/6000HVis 1.0
α4/5000HVis 1.0
α8/6000HVis 2.2
α12/4000HVis 2.5
α22/3000HVi 4.0
α22/4000HVis 4.5
α30/4000HVis 5.5
α40/4000HVis 5.5
α50/3000HVis w/fan 14
α100/2500HVis 11
Incoming DC Power for βi Series
Input Voltage 24VDC (±10%)
Current Requirement (per amplifier):
βi Series 0.9 amps
βHVi Series 0.9 amps
Control Power Specification
The βi and βHVi Series amplifiers require a
24VDC power supply for amplifier control
power. This DC power supply must be
supplied by the user. We recommend the
GE 24VDC power supply, part number
IC690PWR024. The same external DC
power supply can be used to provide
power to multiple amplifiers as long as
the supply is rated for the total current
requirements of all of the amplifiers.
The αHVi series power supplies require
a single phase 200-230VAC control
power input.