ABB 1TGE120021R0010 Fieldbus unit module
The data engineering of the RTU560 can easily
be carried out by the user with the help of the
MS-WindowsTM based tool RTUtil 560 and by MSExcelTM signal lists.
RTUtil 560 is designed to engineer small RTU560,
medium-sized RTU560 with a set of included IEDs,
and also to engineer router RTUs with all the types
of communication links and IEDs used in the customer's network.Process signal mapping to the
different communication protocols is one of the
main tasks needed in hierarchical communication
network structures. The process signals of a small
RTU connected at the lowest level of a network
may be routed via other RTUs on the way up to
the final network control center (NCC). All necessary communication links and parameters are
engineered with RTUtil 560 in one project.
The signal and communication data can be entered
into RTUtil 560 via import of MS-ExcelTM signal
lists.Therefore only limited RTUtil 560 knowledge
is required. The use of MS-ExcelTM functionality
allows quick and easy data entry of large volumes
of process data.To allow adaptations to specific
customer or project requirements,the structure
of the MS-ExcelTM sheets used for data import is
expandable and can also be used for documentation.
The Engineering principle in RTUtil 560 is according to IEC 61346-1 standard.With the RTUtil 560,
separate views for signals,hardware,and communication data is possible.This makes configuration
changes easy.Before generating configuration files,
the RTUtil 560 system carries out an engineering
data consistency check. Any engineering errors
occurring will be recognized and logged in files
with the error location.
The configuration file transfer will be done by
using the integrated web server connected to the
RTU560 MMI interface. The configuration of the
RTU560 can also be carried out from a remote
PC via Internet links or the customer's Intranet.
Download by a network control center via IEC
60870-5-101/104 file transfer protocol is also possible.Upload of the data files is used for reverse
data engineering.
Engineering
Benefits:
• Running on standard MS-WindowsTM
Operating systems (XP,2000 and NT)
• Process data engineering with MS-ExcelTM
possible with limited RTUtil 560 knowledge
• Quick and easy engineering method for
larger projects
• Already existing MS-ExcelTM signal lists can
easily be adapted to the required format
• MS-ExcelTM templates can be used for
documentation
• Engineering and modification efforts
can be reduced considerably
• MS-ExcelTM template adaptable to customers'
requirements
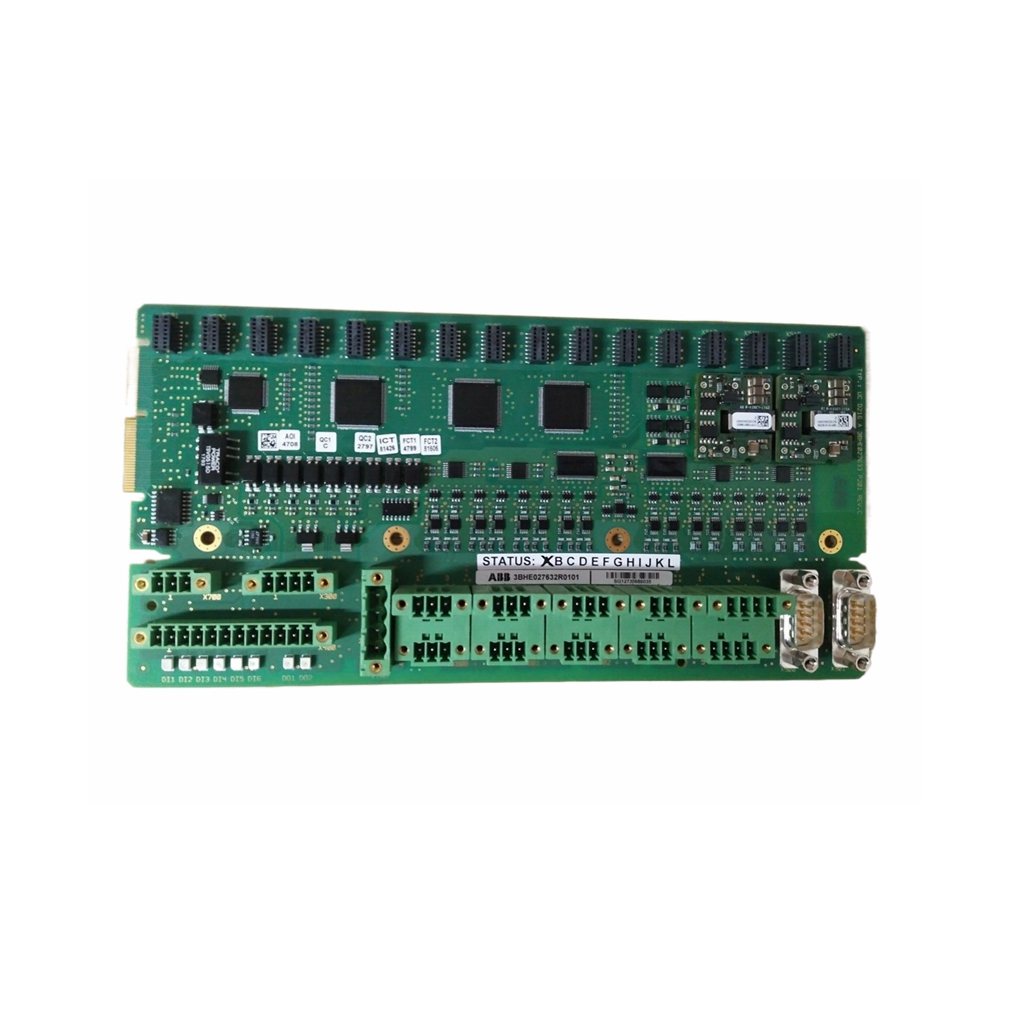
The RTU560 can optionally be equipped with a
Programmable Logic Control (PLC) software
package. This allows sequential control or closedloop application functions that are processed in
parallel to the telecontrol activities.
The PLC programming package fully complies to
the IEC 61131-3 programming standard. The modularity of the RTU560 in hardware and software
allows PLC programs to be run either on the same
CMU central board,parallel to the telecontrol task,
or on a separate CMU central board used only for
the PLC application.PLC programs have access to
all process signal values as well as the process signal qualifiers such as invalid,time,etc..PLC programs running distributed applications may use the
qualifiers for secure and safe operation.
PLC programs update the process signal values via
the process data interface. The telecontrol task will
be informed about changes and updates the new
output values either to the process output boards
or via the communication line to the network control centers and subdevices.
PLC programs are developed by a powerful PLC
programming tool MULTIPROG® wt.
The PLC package allows programming in the programming languages defined in IEC 61131-3:
• Function Block Diagram (FDB)
• Ladder Diagram (LD)
• Sequential Function Chart (SFC)
• Instruction List (IL)
• Structured Text (ST)
The function block RTU library contains function
blocks to interface with the process I/Os values,
attributes and qualifiers. Additionally it is also possible to create user-specific function blocks or
functions for various applications.
PLC functions
Benefits:
• No need of additional PLC systems
• Flexible method to adapt to customer
specific requirements
• Reduced education cost due to compatibility to IEC 61131-3 programming standard
Mechanical Layout
Depending on where the RTU560 is used,it is not
always necessary to support multiple communica tion links.The RTU560 concept allows the configu ration of three types of RTU.
• The Standard RTU560A
• The Compact RTU560C
• The Economic RTU560E
The Compact RTU560C allows a maximum of two
CMU main boards to be plugged into a standard
I/O subrack. The standard version is one CMU
main board with one or two links to the NCCs or
one NCC link and one link for IEDs.The residual
part of the I/O subrack can be used for I/O boards.
The Compact RTU560C also supports the full
volume of I/O boards distributed over the four
peripheral I/O bus segments.
If more communication lines are required,the Stan dard RTU560A must be used.One or two central
communication subracks can be used with their
full range of flexibility and configuration capabili ties.
The Remote Terminal Unit RTU560E is an integral
part of the remote terminal unit RTU560.It is well
suited for applications with small and medium sized datapoint volumes,for instance in local net work stations or in small distribution substations.
Due to the compact design and the flexible confi guration possibilities the RTU560E is suitable for
centralised or de-centralised system architectures.