ABB ACV700 Frequency Converters
This manual describes the ACV 700 drive system to the application
engineers and other persons involved with ACV 700.
The drive has a multidrive configuration. It consists of a supply
section including connection devices (main fuses and main contactor
or circuit breaker), rectifier devices (a diode or thyristor bridge),
capacitors for smoothing of the DC voltage, optional devices, if
specified, and a number of drive sections.
The power range for the supply sections is 40 - 2500 kVA and the
power range for the drive sections is 9 - 2500 kVA.
Depending on the required power and voltage, the drive sections are
based on either an IGBT or GTO thyristor power stage.
The control system is implemented by using the Common Drive
Control, CDC, and the Digital Drive Control, DDC. The basic part of
the CDC is the Application Controller, the APC.
The APC is designed to give a flexible, compact and efficient system
for controlling AC or DC drives. The APC is programmable by using
function blocks.
The DDC performs the inverter control functions.
Programming can be done using two alternative tools, the Function
Chart Editor, FCE or the AdvaBuild for Windows, the Drives version.
Various drive configurations are possible using one or multiple APCs
and their communication capabilities.
In small systems one APC is connected to up to four Digital Drive
Controllers (DDC). The drive configuration can be used in master/
follower applications when the master drive is of moderate complexity
and the followers fairly simple. A consequence of multiplexing is that
the performance of the drive controller interface decreases
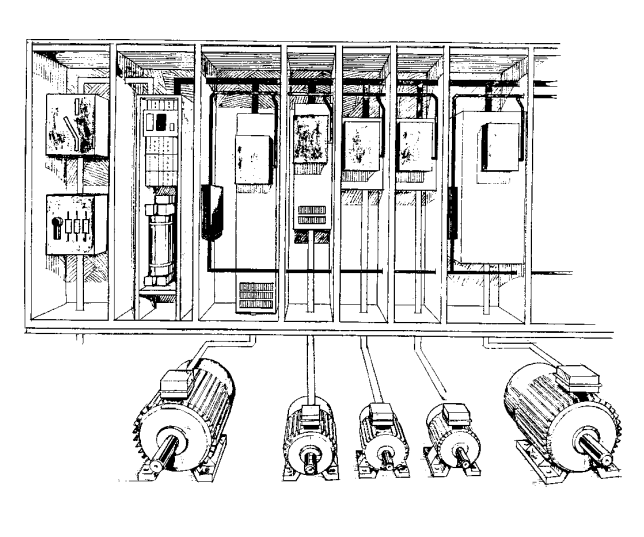
Figure 1 - 1 Small drive system.
In distributed multicontroller systems, several APCs are interconnected by Advant Fieldbus 100 (AF100). Common control functions
can be distributed to separate nodes. No overriding automation system is used in this configuration, but one or several application controllers can communicate with external systems over communication
boards.
A personal computer (PC) can be connected through one of the
APCs and can be used for tool functions.
Mains Connection
Voltage, 3 phase: UN = 400 V (380, 415 V) ± 10 %
UN = 500 V (440, 460 V) ± 10 %
UN = 690 V - 10 %, + 6 % (575, 660 V ± 10 %)
Frequency: 50 Hz or 60 Hz ± 3 %
Fundamental power factor 0.97 to 0.99
Total power factor: 0.93 to 0.95 (theoretical maximum)
Efficiency at Rated Power > 98 %
Motor Connection
Voltage, 3 phase: 0 - 105 %UN
Frequency: 0 to ± 200 Hz
Frequency resolution: 0.01 Hz
Static speed control accuracy
with pulse encoder feedback: 0.01 %
without feedback (motor slip): 0.5 - 3 %, can be reduced by slip compensation
Dynamic speed control accuracy: 0.2 - 0.3 % sec at 100 % load step
Load capacity
Continuous: Refer to tables in section 10, inverter sections
Overload: Refer to tables in section 10, inverter sections
Switching frequency
IGBT-inverters: 3 kHz max.
GTO-inverters: 800 Hz max.
Field weakening set point range
Frequency: 10 - 200 Hz
Voltage: 0 - 105 %
Torque step rise time: 5 to 10 ms at 100 % torque reference step (vector
control)
Acceleration time: 200 ms - 600 sec. / 100 Hz
Deceleration time: 200 ms - 600 sec. / 100 Hz
Enclosure
Degree of protection: IP21 (MD-cabinet)
IP00 (module)
Paint colour: light beige, NCS 1704-Y15R
Environmental limits
Stationary use: Ambient air temperature: + 5 to + 40 ° C (+ 45 ° C)
Storage: Ambient air temperature: - 25 to + 55 ° C
Transportation: Ambient air temperature: - 40 to + 70 ° C
Cooling method: dry clean air, integral fan
Corrosion severity level of
cooling air: up to G1 as specified in ISA-S71.04
Relative humidity: ≤ 95 %, no condensation allowed
Altitude: ≤ 1000m ASL, 100 % load capacity
Operating air temperature +5 °C to +40 °C, IEC 68
Storage air temperature -25 °C to +55 °C, IEC 721
Transport air temperature -40 °C to +70 °C, IEC 721
Mains voltage variation VDE 0160 excluding short time overvoltage.
UN = 400 V (380 V, 415 V) ± 10 %
UN = 500 V (440 V, 460 V) ± 10 %
UN = 690 V - 10 %, 6 %(575 V, 660 V ± 10 %)
Degree of protection by enclosure IP 21 (optional IP 41), IEC 529
General IEC 439-1
Clearances and
creepage distances IEC 664-1
Safety of machinery IEC 204-1 (EN 60 204)
Drawings IEC 113-8
Symbols IEC 617-1
Drive Products and Systems division of ABB Industry Oy has ISO
9001 certification.
Specified Electrical
Environmental and
Safety Parameters
Environmental
Conditions
Electrical
Conditions
Safety
Documentation
Product
Certification